The centralized cooling plant considered equips an important office building in Brussels. This 54 000 mP2P building has a design cooling demand of about 5.7 MW. To meet the cooling loads, the chilling plant can use five counterflow cooling towers, four twin-screw chillers and four tanks with encapsulated ice. The purpose of the commissioning is to check the thermal performance of the primary equipment and to use the simulation tools to give a correct forecast of the cooling capacity available as well as the cooling energy stored in the ice storage tanks. The cooling plant has been operating for three years. Therefore, this commissioning has been submitted to two important constraints : the freedom to test the chilling plant in various configurations is very limited and one can only deal with the information provided by the BEMS (Building & Energy Management System) and the control display of the chillers. Since no flow meter equips the cooling plant, a series of energy and mass balances based on the data provided by the acquisition system are done. The analysis of these data points out the inaccuracy of several temperature sensors. As a result, this inaccuracy is transferred to the flow rates given by the energy balances (especially at low cooling loads). To overcome partially this problem, a hydraulic analysis of the cooling plant is done thanks to the data provided by the installers. The flow rates given by the hydraulic simulation and the data provided by the control panels of the chillers are then used to evaluate the thermal performance of the chillers. These results are confronted with the results of the simulation of the chillers. Such as for the other components of the cooling plant, the model of chiller is identified on the basis of the information given by the manufacturer. The whole centralized cooling plant can also be simulated in all its operating modes. The paper shows how the simulation of one of these modes, the discharging, is validated.
Commissioning of a centralized cooling plant
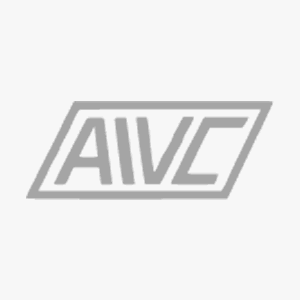
Year:
1997
Bibliographic info:
Belgium, Proceedings of Clima 2000 Conference, held Brussels, August 30th to September 2nd 1997